Ergonomics is the study of people at work. More specifically, it is the science of designing workplaces in a manner that reduces risk of musculoskeletal injury while improving work performance. All of this is based on understanding human physical and psychological abilities and limitations, and then applying this knowledge to the design of the man-made environment.
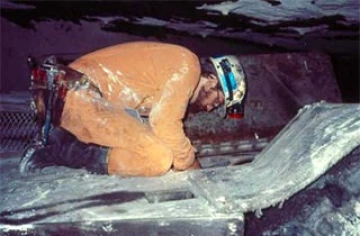
A substantial amount of information regarding ergonomics is available from NIOSH, various universities, and the Board of Certified Professional Ergonomists. This primer provides a summary of ergonomics principles and practices.
Ergonomics Overview
Ergonomics (or human factors engineering, as it was originally known in the USA) historically involved the study and improvement of human-machine systems. The desire to improve human performance can be traced to pre-historic times, through changes in tools and weapons which improved hunting and warfare performance. The modern field of ergonomics developed out of military necessity during the Second World War. Early in the war, pilots and operators were commonly blamed for the failings of their airplanes, tanks, and ships. As losses mounted, the mismatch between operator abilities and equipment characteristics became painfully clear: The failures were often due to factors beyond the operators' control. Tactical necessity compelled the world's militaries to re-think design and build their equipment around the ergonomic needs of their soldiers.
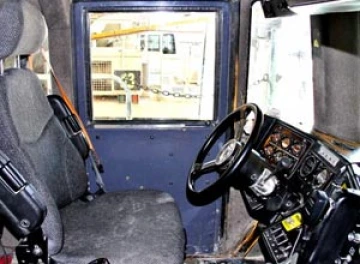
Eventually the desire for better human-machine performance spread through industry. A new emphasis on injury reductions led to further studies which considered the mismatch between people and tasks. Much of the early work on human physical capability was done in Europe; however, by the 1970s, U.S. researchers were focused on the importance of job and task design as a means to limit musculoskeletal injuries. Back injuries were of particular interest, because they were the most frequent and costly. Over time, researchers have come to understand the significant relationship between human capacity — both physical and psychological — and task-induced external load. As a result, interests have gradually expanded to consider all forms of musculoskeletal injury.
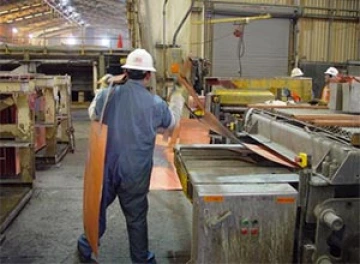
Musculoskeletal injury remains the focus of ergonomics today. In designing equipment or tasks, there are many key questions to consider: What is reasonable to expect from people? How much can an individual safely lift, push, or pull without being overloaded? How do overload constraints vary with body posture and time on task? How variable is that within the individual (day-to-day variability due to fatigue, yesterday's activity, etc.) and between individuals (the large young active male versus the small elderly sedentary female)? How long can an individual focus on a task, and what factors affect focus? What can people hear, see, feel, or otherwise perceive about their jobs, and how does this perception change with time? As we understand these and related ergonomics factors, we can design jobs within the capacity of the workforce, and therefore yield more consistent performance with fewer musculoskeletal injuries.
Ergonomics and Mining
How does this relate to mining? In mining, the man-made environment encompasses the tools, equipment, and job/task designs on the mine site.
Consider the variety of tools used by mechanics to maintain the haul trucks — welders, wrenches, chippers, hammers, screwdrivers, pneumatic versions of these tools, testers, etc. Now consider how these tools are used. What forces are the mechanics required to exert to control and work with the tools? What postures are required of the mechanics during the exertion of these forces, and how does the posture change the risk of musculoskeletal injury? How often does this tool have to be used each day, or how often does the task have to be done? How much does the mechanic (or the supervisor) understand about how posture, force, and frequency combine to raise/lower the injury risk? How much time has been spent by management, the supervisor, or even the mechanic in evaluating the interactions between the mechanic, the equipment being worked on, the tool(s) used, the postures selected, the exposure frequency in a given time period, the length of the work and rest periods, and the work environment? Then how much time has been made available (and actually used) to decide how to proceed to minimize the musculoskeletal injury risk given the above risk factors that need consideration.
Now let us expand our consideration to the wide variety of equipment used on a mine site. These include people moving equipment, product moving/material handling equipment, product processing equipment, process control equipment, packaging equipment, office equipment, IT equipment, etc. In the same way as described for the mechanic, people interact with all of this equipment. The design of the equipment, the design of people's interaction with the equipment, and people's individual abilities and limitations determine the extent of musculoskeletal injury risk for each person, as well as how well they are able to perform when using the equipment.
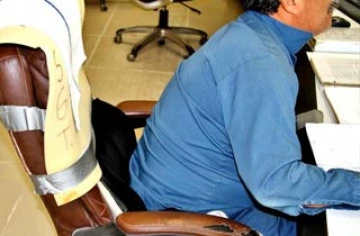
For example, consider a chair. Chairs are used in many places on a mine site (vehicles, offices, control rooms, meeting rooms, etc.) and for many work-related activities. Yet chairs can be the source of many problems: Low back, mid-back, neck, shoulder, arm, and wrist pain, as well as fatigue, eyestrain, and headaches. Some of the above can be serious enough to result in recordable injuries, and all affect the quality and quantity of a persons production. Like any other piece of equipment, it needs to be matched to the user and the task. Even the simple, "cheap", conference room chairs have a purpose. If they result in discomfort, people are distracted and the training or meeting time is of less value. Note the back and neck posture in the photo. The operator is intently focused on a control panel, holding his body in tension as he tries to control a process. He wears glasses and complains of eyestrain, neck pain, and low back pain. These complaints are unsurprising. The mine operator ultimately re-configured these workstations. How much time and analysis went into the selection of chairs to match the task, the people using them, and the effect on those chairs (i.e. discomfort, fatigue, and reduced performance)? These are the key considerations that will impact overall productivity — far more than the cost savings of a few office chairs purchased at a "good" price.
Ergonomics Example
Consider this ergonomic problem and its very simple solution:
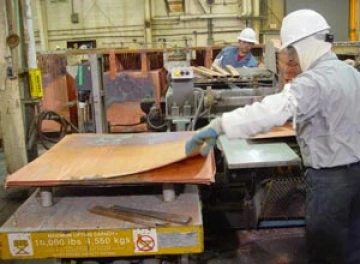
Consider a person feeding copper sheets into a press. The problem is the sheets are stuck together and, being flat, they are hard to separate and pick up. Workers must slap the surface hard to jar the sheets loose, so they can be separated and picked up. Hand injuries are likely from the repetitive slapping, and this process slows down the work by 30% to 40%.
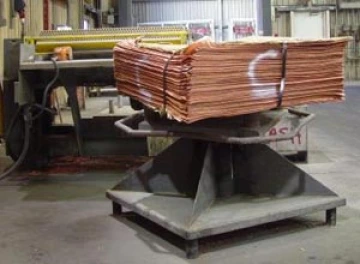
Ergonomic solutions are often simple and cost effective. They require listening to the people doing the work, understanding their constraints, and applying lateral thinking.